來源:互聯(lián)網(wǎng) 由深圳長源興科技有限公司收集整理
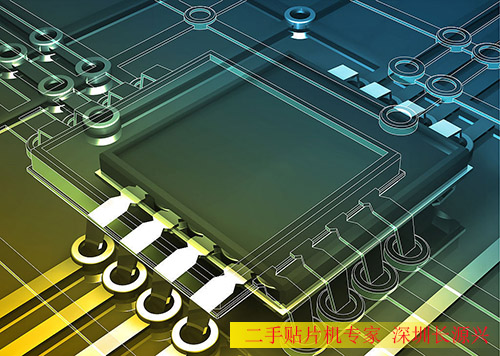
電子元器件是電子信息設(shè)備的細胞,板級電路組裝技術(shù)是制造電子設(shè)備的基礎(chǔ)。不同類型的電子元器件的泛起總會導(dǎo)致板級電路組裝技術(shù)的一場革命。60年代與集成電路興起同時泛起的通孔插裝技術(shù)(THT),跟著70年代后半期LSI的蓬勃發(fā)展,被80年代登場的第一代SMT所代替,以QFP為代表的周邊端子型封裝已成為當(dāng)今主流封裝;進入90年代,跟著QFP的狹間距化,板級電路組裝技術(shù)面對挑戰(zhàn),盡管開發(fā)了狹間距組裝技術(shù)(FPT),但間距0.4mm以下的板級電路組裝仍舊有很多工藝面對解決。作為最理想的解決方案90年代前半期美國提出了第二代表面組裝技術(shù)的IC封裝一面陣列型封裝(BGA),其近一步的小型封裝是芯片尺寸的封裝(CSP)是在廿世紀90年代未成為人們的關(guān)注的焦點,好比,組裝實用化難題的400針以上的QFP封由組裝輕易的端子間距為1.0-1.5mm的PBGA和TBGA代替,實現(xiàn)了這類器件的成組再流。特別是在芯片和封裝基板的連接上采用了倒裝片連接技術(shù),使數(shù)千針的PCBA在超級計算機、工作站中得到應(yīng)用,叫做FCBGA,正在開始實用化。第三代表面組裝技術(shù)直接芯片板級組裝,但是因為受可靠性、本錢和KGD等制約,僅在特殊領(lǐng)域應(yīng)用,IC封裝的進一步發(fā)展,99年底初露頭角的晶片封裝(WLP)面陣列突出型FC到2014年期待成為對應(yīng)半導(dǎo)體器件多針化和高機能化要求的第三代表面組裝封裝。
IC封裝一直落后于IC芯片本身固有的能力。我們但愿裸芯片和封裝的芯片之間的機能縫隙減小,這就促進了新的設(shè)計和新的封裝技術(shù)的發(fā)展。在新的封裝設(shè)計中,多芯片封裝(CSP)包含了一個以上的芯片,相互堆積在彼此的頂部,通過線焊和倒裝片設(shè)計(在倒裝片上線焊,在線焊上倒裝片,或在線焊上線焊)實現(xiàn)芯片間的互連,進一步減少了器件重量和所占空間)。
因為尺寸和本錢上風(fēng),晶片級CSP(Wafer-levelcap)將被進一步開發(fā),這種技術(shù)是在晶片切割成小方塊(芯片)之前,就在芯片上形成第一級互連和封裝I/O端子,這不但縮短了制造周期,其I/O端子分為面陣列型和周邊型(依據(jù)I/O端子的分布)兩種類型;前者,EIAJ的端子間距0.8mm以下,外型尺寸為4mm-21mm的超小型封裝作為尺度,主要合用于邏輯和存貯器件,后者是SON和QFN等帶周邊端子的無引線小型化封袋,主要合用于存貯器和低檔邏輯器件。自從90年代初CSP問世以來,提出了各種各樣的結(jié)構(gòu)形式,現(xiàn)在以面陣列型的FBGA是主流,第一代FBGA是塑料類型的面朝下型,第二代FBGA是載帶類型的面朝下型,都采用了引線框架塑模塊、封裝,而新一代的FBGA是以晶體作載體進行傳送,切割(劃線)的終極組裝工藝,即WLP方式,取代了以前封裝采用的連接技術(shù)(線焊、TAB和倒裝片焊),而是在劃線分割前,采用半導(dǎo)體前工序的布線技術(shù),使芯片襯墊與外部端子相連接,其后的焊料球連接和電氣測試等都在晶片狀態(tài)下完成,最后才迫行劃線分割。顯然用WLP方式制作的是實際芯片尺寸的FBGA,形狀上與FC無區(qū)別。
總之,PBGA、TBGA、FBGA、(CSP)和FC是當(dāng)今IC封裝的發(fā)展潮流。表1和表2分別示出了這些封裝的發(fā)展動向。在21世紀的前15年,第三代表面組裝封裝將會迅速發(fā)展,圍繞高密度組裝,封裝結(jié)構(gòu)的多樣化將是21世紀初IC封裝最明顯的特點。LSI芯片的疊層封裝、環(huán)形封裝:還有,將泛起新的3D封裝,光一電子學(xué)互連,光表面組裝技術(shù)也會蓬勃發(fā)展。系統(tǒng)級芯片(SOC)和MCM的系統(tǒng)級封裝(MCM/SIP)跟著設(shè)計工具的改善,布線密度的進步,新基板材料的采用,以及經(jīng)濟的KGD供應(yīng)的普及,將進一步得到開發(fā)和進入實用階段。
無源封裝
跟著產(chǎn)業(yè)和消費類電子產(chǎn)品市場對電子設(shè)備小型化、高機能、高可靠性、安全性和電磁兼容性的需求,對電子電路機能不斷提出新的要求,從20世紀90年代以來,冶式元件進一步向小型化、多層化、大容量化、耐高壓和高機能方向發(fā)展,同時跟著SMT在所有電子設(shè)備中的推廣應(yīng)用,世界范圍片式元件的使用量迅速增加,現(xiàn)在年消耗片式元件達到1兆只,無源元件對IC的比率一般大于20.因為需要如斯大量的分立元件,所以分立元件支配終極PCB組件的尺寸;另外,片式無源元件用量的劇增使貼裝工藝中的瓶頸經(jīng)片式元件的貼裝更難解決,導(dǎo)致出產(chǎn)線失去平衡,設(shè)備利用率下降,本錢進步,同時片式元件供應(yīng)時間占用出產(chǎn)線時間的30%,嚴峻影響出產(chǎn)量的進步。解決這些題目的有效辦法就是。實現(xiàn)無源元件的集成。
集成無源元件有以下幾種封裝形式:
陣列:將很多一種類型的無源元件集成在一起,以面陣列端子形式封裝;
網(wǎng)絡(luò):將很多混合電阻和電容集成在一起,以周邊端子形式封裝;
混合:將一些無源元件和有源器件混合集成進行封裝;
嵌入:將無源元件嵌入集成在PCB或其它基板中;
集成混合:所集成的無源元件封裝在QFP或TSOP格局中。
這些無源封裝的推廣應(yīng)用,可以有效地解決貼裝:瓶頸,改善SMT出產(chǎn)線平衡,降低本錢,進步產(chǎn)量,進步組裝密度。
提高前輩板級電路組裝工藝技術(shù)的發(fā)展
電路組裝技術(shù)的發(fā)展在很大程度上受組裝工藝的制約同,假如沒有提高前輩組裝工藝,提高前輩封裝難以推廣應(yīng)用,所以提高前輩封裝的泛起,必定會對組裝工藝提出新的要求。一般來說,BGA、CSP和MCM完全能采用尺度的表面組裝設(shè)備工藝進行組裝,只是因為封袋端子面陣列小型化而對組裝工藝提出了更嚴格的要求,從而促進了SMT組裝設(shè)備和工藝的發(fā)展。
1. 漏板設(shè)計和印刷
在提高前輩組裝技術(shù)中,焊膏是廣泛采用的主要焊接材料,焊膏沉積采用漏板印刷技術(shù)。在漏板印刷工藝中,刮板葉片將焊膏推入漏板開孔轉(zhuǎn)移到電路板上,影響焊膏印刷機能的四個因素是:(1)漏板開孔尺寸,決定了印刷膏的量;(2)焊膏脫模,在特定焊膏情況下,開孔壁和幾何外形和光潔度影響焊膏脫模;(3)開孔的縱橫比和面積比,開孔的寬度和長度之比,啟齒面積和開孔壁面積之比;通常設(shè)計規(guī)則是縱橫31.5,面積0.66;但是對于光滑的錐形開孔壁,這兩個比分別為1和0.44就能獲得良好的焊膏脫模。在設(shè)計漏板厚度時,這個兩個比率就是重要的設(shè)計規(guī)則。當(dāng)開孔長度大于其寬度的5倍時,縱橫比是主要設(shè)計規(guī)則(QFP時),當(dāng)開孔長度即是寬度時,面積比是更精確的設(shè)計規(guī)則(采用球柵陣列焊盤時)。(4)焊膏印刷精度,當(dāng)在電路板上印刷焊膏時,電路板上的焊盤圖形和漏板上的開孔在尺寸和位置上必需完全相符,漏印的焊膏立方塊必需無變形。 BGA、CSP和FCOB的板級組裝極用共晶焊料合金,BGA采用普通SMT用焊膏就可以知足要求,但對于CSP和FCOB I/O端子比通SMT封裝提供的焊接面積小,所以要求漏板啟齒更小,必需采用小于40um,顆粒尺寸的精細焊膏。它們的漏板設(shè)計和制造要求與窄間距器件一樣嚴格.BGA、CSP和倒裝片組裝的漏板一般要求采用激光或電鑄成型工藝,而后進行電拋光,固然制造本錢高,但一致性超過化學(xué)蝕刻漏板;有時還要求渡鎳,并采用錐形開孔,以便進步孔壁光潔度,有利于焊膏脫模,漏板啟齒尺寸,一般比電路板上的焊盤尺寸略小為宜,啟齒以略微增加印刷的焊膏量。
漏板厚度是漏板設(shè)計的主要指標,對于BGA要求采用的漏板厚度為0.13-0.15mm,CSP用的漏板厚度是0.10-0.13mm。因為漏板較薄,印刷時要防止從開孔中取出焊膏。組裝BGA和CSP時,通常都按1對1的比例印刷;但對于CSP,實際印刷要比突出尺寸大0.05-0.076mm,使再流焊后器件支撐高度略高些,以進步熱適應(yīng)性,并可繼承選用三類焊料粉末。對于采用0.3mm直徑突出的CSP推薦采用0.3-0.6mmr 矩形開孔。0.36mm的啟齒是采用三類焊料粉末最小可能的啟齒尺寸,以便進行一致性和重復(fù)性好的印刷。假如印刷0.25mm的矩形或圓形開孔將要求采用IV 類焊料粉末。
為了適應(yīng)電子產(chǎn)品的輕薄小型化、高密度、多功能和高可靠性的要求,混合組裝技術(shù)仍舊是21世紀初電路組裝發(fā)展的趨勢之一。不僅通孔器件和SMD混合組裝,而且跟著以倒裝片為核心的直接能組裝技術(shù)的推廣應(yīng)用,將會泛起通孔元器件、SMD或倒裝片在統(tǒng)一電路板上的組裝,這就是對漏板設(shè)計和印刷提出了新的挑戰(zhàn)。有不同的組裝工藝完成混合電路組件的組裝,其中采用再流焊接技術(shù)是比較理想的工藝方法,以便充分施展SMT出產(chǎn)線的作用,降低本錢,進步出產(chǎn)率,有幾種漏板設(shè)計和印刷方法可供選擇,其中比較理想的是雙漏板印刷。
提高前輩的封裝對焊膏的印刷精度要求比普通SMT更加嚴格,所以應(yīng)該采用視覺系統(tǒng)的高精度印刷機完成焊膏的印刷功課。這類印刷也有高檔和中檔之別,要根據(jù)用戶的需要和可能選購。印刷功課開始,首先要完成漏板和電路板的對準,借助視覺系統(tǒng)可以很利便地實現(xiàn)漏板開孔和電路板上焊盤圖形的精確對準。高級對準系統(tǒng)具有全集成圖像識別處理功能,可以實現(xiàn)快速而正確的圖像對準,確保高質(zhì)量的焊膏印刷和高和出產(chǎn)效率。印刷和第二個題目是根據(jù)電路板類型、刮板類型和所用焊膏設(shè)定印刷高度、刮板壓力和角度、印刷還度等印刷參數(shù);另外環(huán)境溫度和相對濕度也是重要的印刷參數(shù);提高前輩封裝對印刷參數(shù)偏差要求嚴格,必需借助印刷機的計算機控制系統(tǒng)進行正確而嚴格控制。更高檔的印刷機上還裝有2D和3D激光檢測系統(tǒng),檢查印刷質(zhì)量,知足了提高前輩封裝對印刷精度的要求。
2. 貼裝技術(shù)
盡管陣列封裝明顯地使用貼裝位置規(guī)范限制加寬,但是因為這類封裝的I/O端子在封裝體下面呈陣列分布,所以精確貼裝這類器件最先決前提是檢查焊料球的存在與否和間距,檢查焊料球外形態(tài)。這就要求貼片機的視覺系統(tǒng)能根據(jù)球的外形質(zhì)量因數(shù)和建立焊料球畸變認可等級實現(xiàn)這種功能。。二維寬度和外形質(zhì)量因素測試是檢查整個球體積和畸變的可靠方法,所以,貼裝機的視覺系統(tǒng)應(yīng)具有合適和分辨率,以便搜集和形成最佳影響;為此就必需采用合適的外部照明和遠心焦蘭光學(xué)系統(tǒng),并通過大深度聚焦提供恒定放大倍數(shù),以便確定球的存在和精確尺寸;采用LED(發(fā)光二極管)提供最佳照明前提,特別需要輪廓對中的背照明和公道選用明視場和前照明,前照明應(yīng)采用三個可編程光源給每封裝形式提供特殊的理想照明,以便在焊球結(jié)構(gòu)和背影環(huán)境之間形成適當(dāng)反差,提供精確對中的光學(xué)前提。視場應(yīng)適合觀察物的特微和位誤差要求,以便能確定良好的、出缺陷的損壞的焊料球之間的差別。處理全部提高前輩封裝的高機能貼裝機必需擁有兩臺元器件攝像機(一臺尺度型和一臺倒裝片用攝像機)。BGA器件的精確定可以根據(jù)每個角落的5個球發(fā)現(xiàn)球柵的整體位置和取向,并根據(jù)BGA樹檢索算法和采用模板比較算法確定的位置;然后借助于灰度級機器視覺系統(tǒng)和計算機控制最后實現(xiàn)BGA的精確對準和貼裝。另外還可以在PCB上設(shè)置器件局部基準標記,以便進步貼裝精度。BGA的貼裝誤差主要來自接觸表面的非共面性,所以在貼裝操縱期間必需建立和維持接觸表面的共面性,采用自動準直儀,使貼裝機的運動保持共面性。